|
|
Monicor-2M indicator is supplied with:
|
|
- Nonvolatile information tank for 16,000 measurements
- Electronic timer
- Device-to-computer connection port
- Electronic commutator for standalone measurement and storage of data coming from from 4 sensors
- Solution ohmic resistance compensator. This helps to increase the accuracy of measurements in media with high ohmic resistance, for instance, in oil emulsions or fresh water
|
|
The device has a manual mode for memory search and indication of corrosion rate from each channel in automated measurement mode. The device’s internal program is currently being upgraded with new modes and will be updated on previously purchased devices at no cost.
|
|
The device is connected to a field sensor and takes measurements in a standalone mode, which allows to detect deviations in medium corrosion activity and corrosion inhibitors protective capability during the whole period of standalone operation (over 1000 measurements, using battery supply). Corrosion rate variations in time are represented on the computer in table and graph forms.
|
|
Data acquisition program for data importing, registering and analyzing has been developed for the device. The program can be optionally expanded with new features. The program also allows to export the received data to MS Excel and *.csv format text files. The exported files containing measurement results allow to download the received data to the “Extra” program.
|
|
Permanent monitoring allows to promptly detect the factors that influence the corrosion process and to optimally select protective doses of inhibitors, which helps to reduce operating expenses on anti-corrosive protection. Working experience proves that permanent monitoring allows to receive the corrosion rate data that are much more reliable than those received during one-time measurements.
|
|
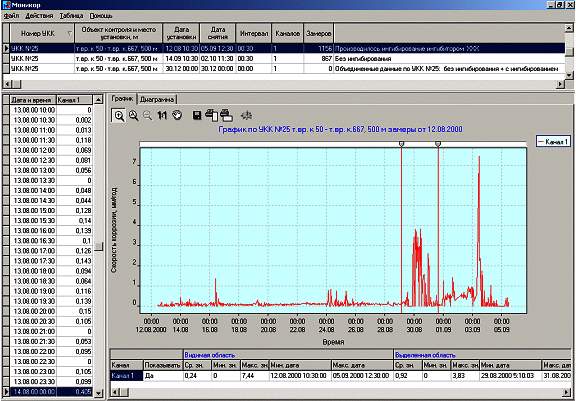 |
|
|
The diagram presented in the main window of the Monicor-2M data acquisition and processing program is received during the corrosion monitoring test on inhibition of a gaslift sector at one of the Western Siberian enterprises. The corrosion rate was between 1-2 mm/year. The analysis of the diagram showed that very high corrosion rates (up to 1 mm/year in the period of 29.08-03.09) during inhibition resulted from acid treatment of wells conducted at that time. Peak readings up to 0,6 mm/year in the period of 24.08-25.08 were caused by a volume pump maintenance works.
|
|
As we can see from the previous example, stochastic changes of a real corrosion rate in field conditions reduce the value of the data received during one-time measurements done with a regularity of a few days, as it is hard to determine real average corrosion wear and protection effectiveness according to such measurements. To monitor the injection process and control the effectiveness of an expensive reagent (30,000-60,000 rubles a month per one feed point) we recommend equipping each sector to be protected with at least one Monicor-2M-type corrosion gauge.
|
|
The following diagrams show the results of testing of various methods of inhibition treatment of producing wells at one of the Western Siberian OGPD in 2002.
|
|
|
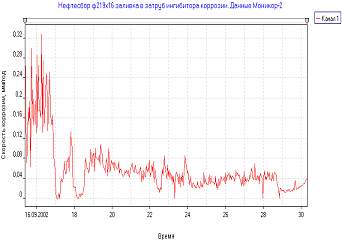 |
|
|
|
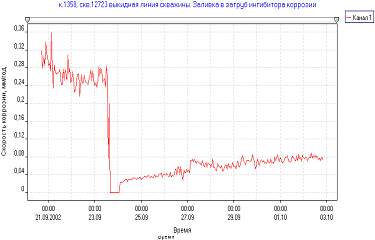 |
|
|
|
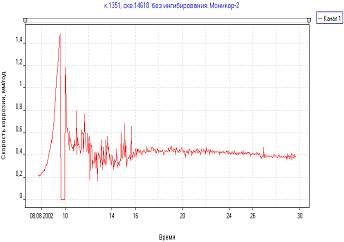 |
|
|
|
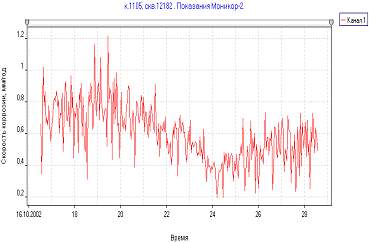 |
|
|
|
Modification of Monicor-2M has been carried out since 2009. During this time, more than 400 devices have been delivered to various consumers, including oil companies, research institutes and enterprises developing new corrosion inhibitors.
|
|
In 2003 we are planning to finish the development of an automatic radio control system (as part of the Monicor-2 corrosion gage) for controlling the productivity of volume pumps based on the processing of readings of corrosion rate remote sensors. Testing procedure is set forth in State Standard (GOST) 9.514-99.
|